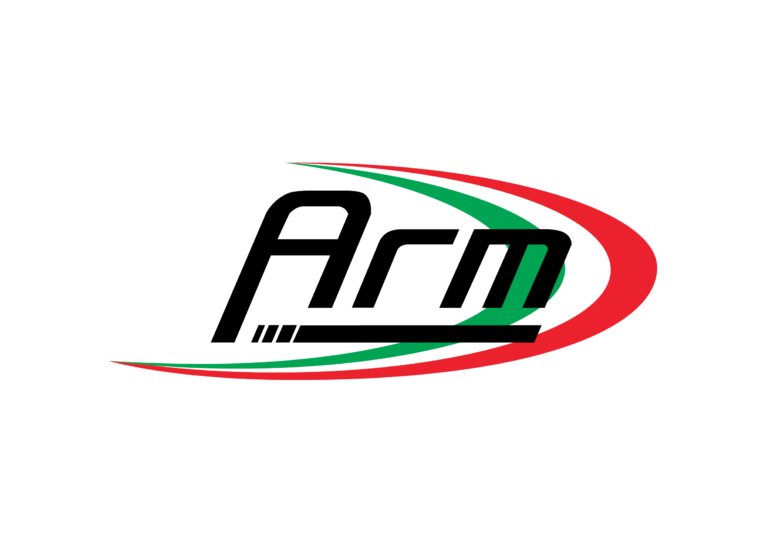
ROBOT FEATURES
- Fanuc M-20iD25
- Payload 25 kg
- Max reach 2.000mm, center tool point
- Max speed (J6) 720°/s
- Repeatability +/-0,02mm
- Wrist protection class IP67
- Weight 250 Kg
INTEGRATED TOWER PARTS STORAGE SYSTEM
- Payload 1.000 kilos
- Stack of max 24 trays (depending on the workpieces shape and dimensions)
TROLLEY FEATURES
- Tray dimension 600x400mm
- Max load each tray 40 kilos
- Metal galvanized structure and trays for long lasting
- Trays quick locking system
GRIPPER FEATURES
- 2-fingers gripper for rectangular shapes
- 3-fingers gripper for round shapes
- 2-fingers gripper for long shafts
- Customized gripper for specific shapes
- Air blow system
- Quick change system for gripper
- Low air pressure detection
SAFETY FEATURES
- Fanuc Dual Check Safety System integrated with laser scanner
- Pneumatic or servo-motor driven CNC machine door opener with integrated safety circuit if predisposed
CONTROL UNIT
- Controller R30iB-PLUS
- Intuitive programming
- Friendly interface
- Fanuc collaborative functions
- Touchscreen
- Machine utilization statistics
- Intelligent maintenance prediction software
- Eccentric loading and unloading mode
- Park positioning function
- Tower full handling
ADDITIONAL WORKING STATIONS
- Parts unloading on box/cage/belt
- Parts positioning on measuring station
- Other tailored customers operations available
CONNECTION PREDISPOSITION
– Teleservice predisposition
– Predisposition for Industry 4.0 connection
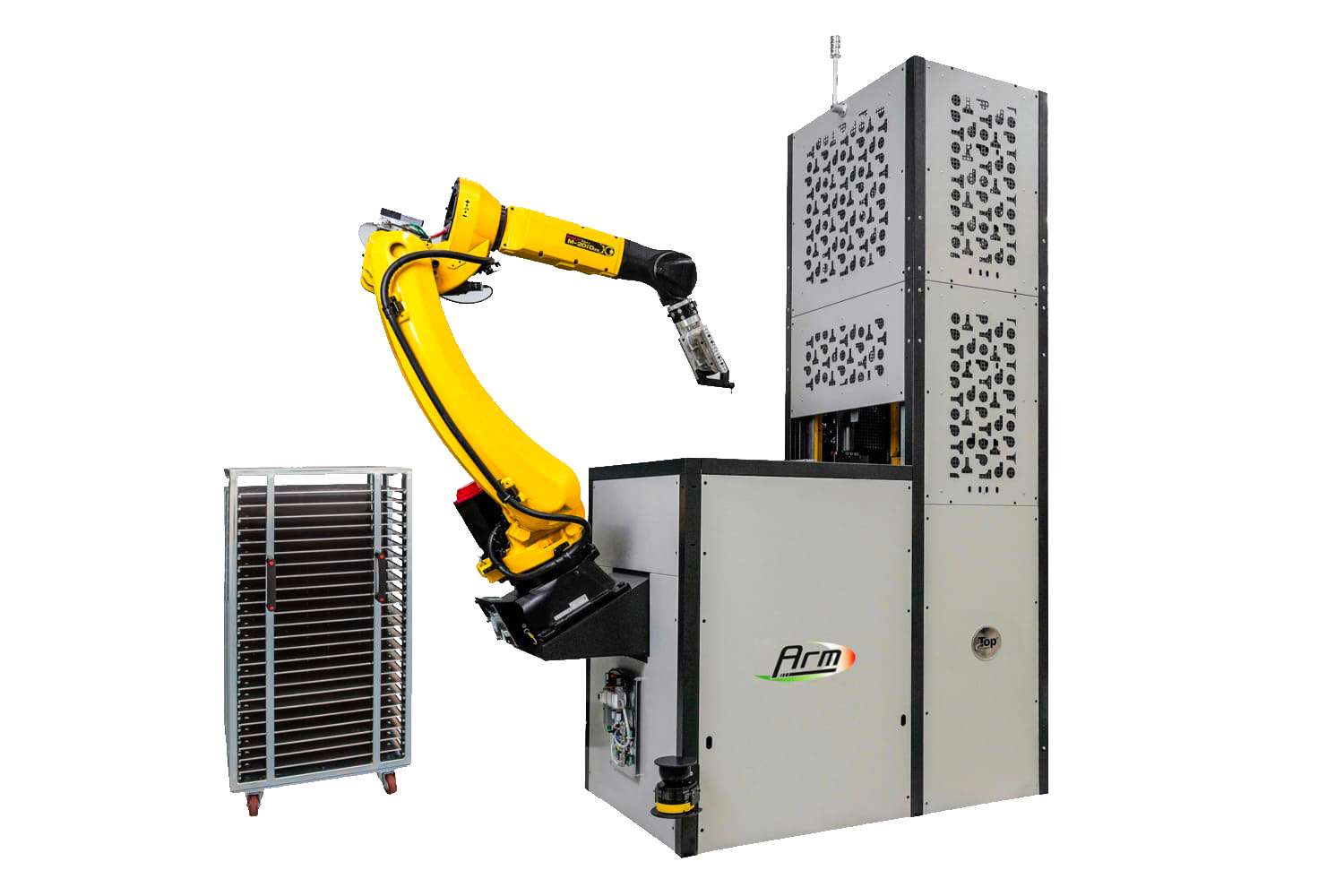
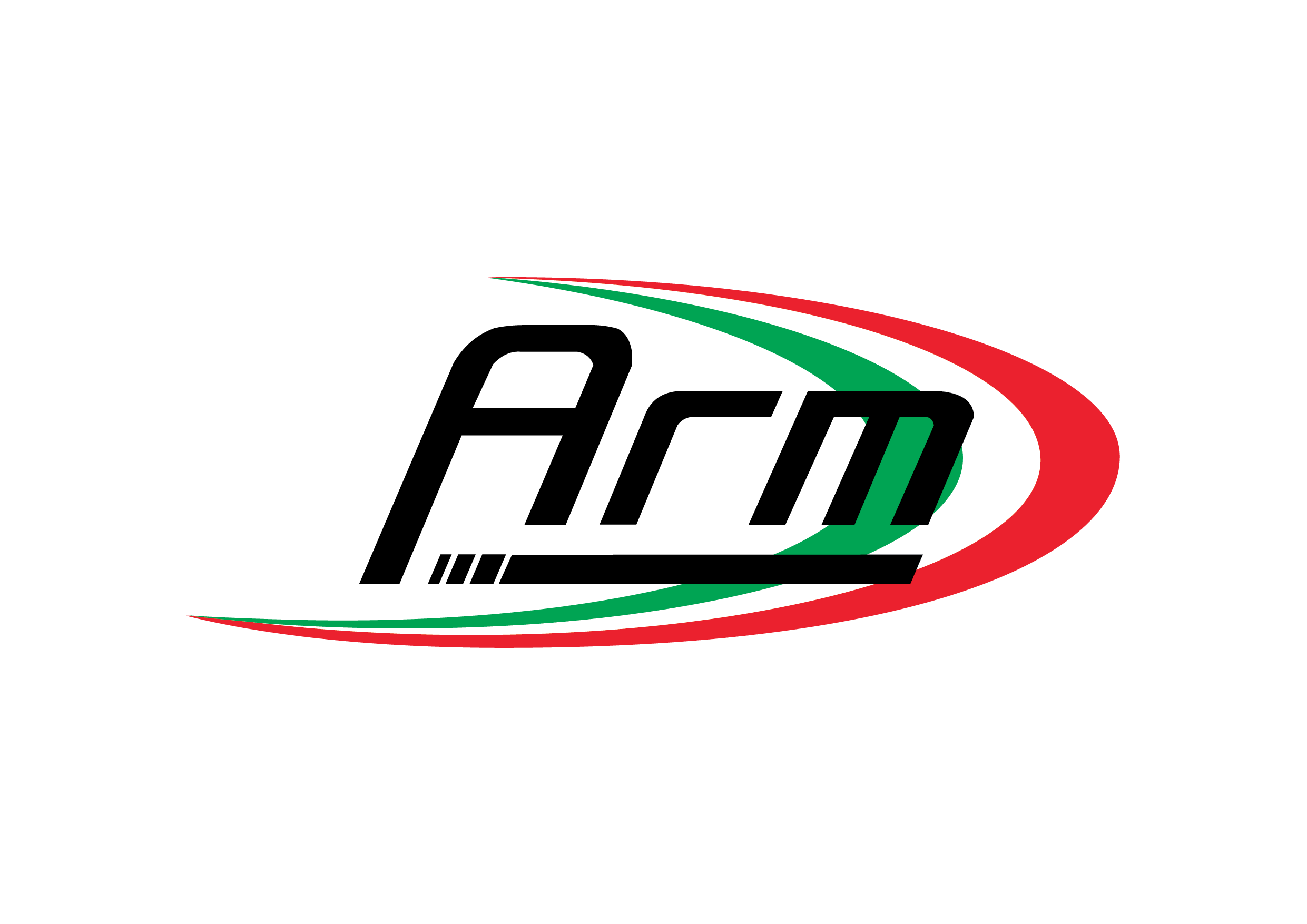
ARM
What is ARM?
ARM is a universal robotic handling “STAND-ALONE” solution with integrated tower parts storage, compact and ready to use. It is designed to be connected to several machine tools as LATHES, GRINDERS, MILLING MACHINES, SAWING UNITS, ecc.
IT IS IDENTIFIED BY THE TERM “STAND-ALONE” BECAUSE EASY AND FAST IN BEING POSITIONED AND QUICKLY CONNECTABLE AMONG SEVERAL MACHINE TOOLS.
ARM is equipped with a FANUC fast accurate anthropomorphic robot, well known through the world for its reliability and solidity, assuring repeatability in the supply of the machine tool.
- The automated warehouse picking system has a maximum capacity of 1.000 kg.
- The storage column counts 24 trays 600mmx400mm each.
- The arm’s payload is up to 25kg, according to the specific need.
- The FANUC Dual Safety Check and a supplementary high sensitive Laser Scanner avoid the presence of any physical barrier within the marshalling area.
- The operator’s access to the modular vertical lift system is straightforward, thanks to the ergonomic trays dispenser mounted on a trolley.
- The open and flexible programming system and the range of accessories ensure the efficient management of a vast series of machined parts.
- The pick and place gripper has a quick release hook-up system
Why do you need ARM?
1. LOWER LABOR COST
- NO operator needed during the whole machining cycle
- Multiple CNC machines handled by one well-trained operator
- Easier workforce managing
2 EXTRA PRODUCTION TIME
- Assured parts production cycle time
- Night shift and weekend shift feasible without additional operators
- Higher reaction speed on urgent job orders
3 HIGHER PRODUCTIVITY LEVEL REACHED
- Even in a one-shift working production plant, the ARM will continue making parts beyond the working day closure
- Skilled operator sets-up the ARM and pass by to the next job order on a different CNC machine
- Increased CNC machine tools park production capacity
THANKS TO ARM YOUR BUSINESS BECOMES MORE PROFITABLE.